
Nairaland Pulse | News

Анатолий Шарий

Реальний Київ | Украина

Мир сегодня с "Юрий Подоляка"

Труха⚡️Україна

Николаевский Ванёк

Инсайдер UA

Реальна Війна | Україна | Новини

Лачен пише

Nairaland Pulse | News

Анатолий Шарий

Реальний Київ | Украина

Мир сегодня с "Юрий Подоляка"

Труха⚡️Україна

Николаевский Ванёк

Инсайдер UA

Реальна Війна | Україна | Новини

Лачен пише

Nairaland Pulse | News

Анатолий Шарий

Реальний Київ | Украина
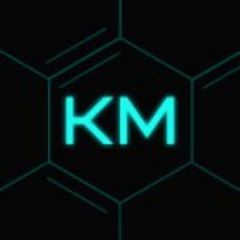
Карбонамама
Technology
Канал, после чтения которого ты говоришь ‘да ну нафиг, вот это да".
Про углепластик без скуки.
Будущее, ошибки, тренды.
Про ДНК материала, призвание и страсть.
Теперь ты тоже- карбонарий.
Про углепластик без скуки.
Будущее, ошибки, тренды.
Про ДНК материала, призвание и страсть.
Теперь ты тоже- карбонарий.
TGlist rating
0
0
TypePublic
Verification
Not verifiedTrust
Not trustedLocationРосія
LanguageOther
Channel creation dateJul 14, 2021
Added to TGlist
Mar 21, 2025Records
27.03.202523:59
959Subscribers19.04.202523:59
100Citation index26.03.202514:32
286Average views per post26.03.202514:32
186Average views per ad post21.03.202512:04
8.43%ER26.03.202514:32
29.85%ERRGrowth
Subscribers
Citation index
Avg views per post
Avg views per ad post
ER
ERR
19.04.202512:58
06.05.202512:21
И короткая памятка, сохраните в Избранном.
Полотняное переплетение (Plain)
Структурные свойства: высокая стабильность в плоскости, умеренная прочность на растяжение и изгиб, низкая драпируемость, низкая устойчивость к ударным нагрузкам и расслоению.
Применение: интерьерные элементы в авиации, панели автомобилей, универсальные конструкционные детали.
Преимущества: недорогое, легко резать и укладывать, равномерные свойства.
Недостатки: низкая ударная прочность, малогибкое, менее эстетичное.
Технологичность: подходит для автоклава, RTM и инфузионных процессов.
Саржевое переплетение (Twill )
Структурные свойства: хороший баланс прочности и гибкости, высокая драпируемость, лучшая ударная стойкость по сравнению с полотняным, характерный диагональный рисунок.
Применение: видимые детали в автомобилестроении и авиации, спортивное снаряжение, изделия сложной формы.
Преимущества: эстетичный внешний вид, гибкость, высокая ударопрочность.
Недостатки: дороже, сложнее в резке и укладке.
Технологичность: хорошо подходит для автоклава, RTM и инфузии.
Атласное переплетение (Satin)
Структурные свойства: высокая драпируемость, гладкая поверхность, хорошая изгибная прочность, умеренная прочность на растяжение, меньший изгиб нитей, чем у полотна и саржи.
Применение: изогнутые сложные формы в авиации и автомобилестроении, премиальное спортивное оборудование.
Преимущества: идеально для сложных форм, гладкий финиш, хороший внешний вид.
Недостатки: низкая стабильность в плоскости, склонность к махрению, плохая размерная стабильность.
Технологичность: оптимально для автоклава и инфузии, особенно в сочетании со сложными формами.
Однонаправленная лента (Unidirectional Tape, UD)
Структурные свойства: максимальная прочность и жёсткость вдоль оси волокна, минимальные свойства поперёк, низкая драпируемость, плохая ударная прочность.
Применение: лонжероны в авиации, лопасти ветряков, велосипедные рамы, высокоэффективное спортивное оборудование.
Преимущества: наивысшая направленная прочность, эффективно для заданных путей нагрузок.
Недостатки: слабость вне направления волокон, трудно укладывать, низкая ударная стойкость.
Технологичность: лучше всего подходит для автоклава, намотки, пултрузии и RTM на линейных изделиях.
Мультиаксиальные ткани.
Структурные свойства: высокая прочность в нескольких направлениях, отличная драпируемость, высокая стойкость к повреждениям, минимальное гофрирование волокон.
Применение: лопасти ветряков, судостроение, крупные конструкционные панели, продвинутые авто- и авиакомпоненты.
Преимущества: индивидуальная ориентация волокон, равномерные многовекторные свойства, высокая ударопрочность.
Недостатки: дороже, сложны в производстве.
Технологичность: подходят для инфузии, RTM и формования крупных деталей.
Практические инженерные выводы
Выбор переплетения напрямую влияет на прочность, гибкость, устойчивость к повреждениям и технологичность.
Полотняное — лучшее решение для простых и недорогих деталей.
Саржа и атлас — идеальны для визуальных или сложных форм.
UD — незаменим для деталей с высокой нагрузкой по оси.
Мультиаксиальные ткани — лучший выбор для крупногабаритных и нагруженных конструкций.
Так, думаю я 100% ответила на вопрос по тканям. В четверг выложу ответ по смолам.
Полотняное переплетение (Plain)
Структурные свойства: высокая стабильность в плоскости, умеренная прочность на растяжение и изгиб, низкая драпируемость, низкая устойчивость к ударным нагрузкам и расслоению.
Применение: интерьерные элементы в авиации, панели автомобилей, универсальные конструкционные детали.
Преимущества: недорогое, легко резать и укладывать, равномерные свойства.
Недостатки: низкая ударная прочность, малогибкое, менее эстетичное.
Технологичность: подходит для автоклава, RTM и инфузионных процессов.
Саржевое переплетение (Twill )
Структурные свойства: хороший баланс прочности и гибкости, высокая драпируемость, лучшая ударная стойкость по сравнению с полотняным, характерный диагональный рисунок.
Применение: видимые детали в автомобилестроении и авиации, спортивное снаряжение, изделия сложной формы.
Преимущества: эстетичный внешний вид, гибкость, высокая ударопрочность.
Недостатки: дороже, сложнее в резке и укладке.
Технологичность: хорошо подходит для автоклава, RTM и инфузии.
Атласное переплетение (Satin)
Структурные свойства: высокая драпируемость, гладкая поверхность, хорошая изгибная прочность, умеренная прочность на растяжение, меньший изгиб нитей, чем у полотна и саржи.
Применение: изогнутые сложные формы в авиации и автомобилестроении, премиальное спортивное оборудование.
Преимущества: идеально для сложных форм, гладкий финиш, хороший внешний вид.
Недостатки: низкая стабильность в плоскости, склонность к махрению, плохая размерная стабильность.
Технологичность: оптимально для автоклава и инфузии, особенно в сочетании со сложными формами.
Однонаправленная лента (Unidirectional Tape, UD)
Структурные свойства: максимальная прочность и жёсткость вдоль оси волокна, минимальные свойства поперёк, низкая драпируемость, плохая ударная прочность.
Применение: лонжероны в авиации, лопасти ветряков, велосипедные рамы, высокоэффективное спортивное оборудование.
Преимущества: наивысшая направленная прочность, эффективно для заданных путей нагрузок.
Недостатки: слабость вне направления волокон, трудно укладывать, низкая ударная стойкость.
Технологичность: лучше всего подходит для автоклава, намотки, пултрузии и RTM на линейных изделиях.
Мультиаксиальные ткани.
Структурные свойства: высокая прочность в нескольких направлениях, отличная драпируемость, высокая стойкость к повреждениям, минимальное гофрирование волокон.
Применение: лопасти ветряков, судостроение, крупные конструкционные панели, продвинутые авто- и авиакомпоненты.
Преимущества: индивидуальная ориентация волокон, равномерные многовекторные свойства, высокая ударопрочность.
Недостатки: дороже, сложны в производстве.
Технологичность: подходят для инфузии, RTM и формования крупных деталей.
Практические инженерные выводы
Выбор переплетения напрямую влияет на прочность, гибкость, устойчивость к повреждениям и технологичность.
Полотняное — лучшее решение для простых и недорогих деталей.
Саржа и атлас — идеальны для визуальных или сложных форм.
UD — незаменим для деталей с высокой нагрузкой по оси.
Мультиаксиальные ткани — лучший выбор для крупногабаритных и нагруженных конструкций.
Так, думаю я 100% ответила на вопрос по тканям. В четверг выложу ответ по смолам.
13.05.202513:07
Исправляюсь.
Часть 1
Для работы с углеволокном применяются различные виды смол, каждая из которых имеет свои особенности и критерии выбора в зависимости от условий эксплуатации и требований к детали.
Основные виды смол для углеволоконных композитов
1. Эпоксидные смолы
- Обеспечивают высокую прочность сцепления с углеволокном, что улучшает механические свойства композита (прочность на сжатие, изгиб и др.).
- Подходят для вакуумной инфузии, имеют среднюю вязкость и хорошую обрабатываемость.
- Могут использоваться для высокотемпературных применений при соответствующей модификации.
- Недостаток: чувствительны к ультрафиолету, требуют защитного лака при наружном применении.
2. Полиэфирные смолы
- Наиболее распространены и дешевле эпоксидных.
- Хорошо подходят для массового производства, быстро отверждаются, устойчивы к коррозии и имеют приемлемую термостойкость.
- Механические свойства хуже, чем у эпоксидных смол.
- Используются в транспортных и строительных профилях, где не требуется высокая прочность.
3. Винилэфирные смолы
- По свойствам занимают промежуточное положение между эпоксидными и полиэфирными.
- Обладают улучшенной ударопрочностью, коррозионной стойкостью и термостойкостью (до 105-121 °С, есть модификации для более высоких температур).
- Хорошо сопротивляются кислотам, щелочам и растворителям.
4. Специализированные смолы
- Фенольные смолы - высокотемпературные, огнестойкие, с хорошей химстойкостью.
- Фурановые смолы - для агрессивных химических сред, выдерживают до 121°С, но требуют аккуратного отверждения.
- Цианат эфирные, полиимидные и бисмалеимидные смолы - для особо высокотемпературных и технически сложных применений.
Вторая часть ответа- завтра.
Часть 1
Для работы с углеволокном применяются различные виды смол, каждая из которых имеет свои особенности и критерии выбора в зависимости от условий эксплуатации и требований к детали.
Основные виды смол для углеволоконных композитов
1. Эпоксидные смолы
- Обеспечивают высокую прочность сцепления с углеволокном, что улучшает механические свойства композита (прочность на сжатие, изгиб и др.).
- Подходят для вакуумной инфузии, имеют среднюю вязкость и хорошую обрабатываемость.
- Могут использоваться для высокотемпературных применений при соответствующей модификации.
- Недостаток: чувствительны к ультрафиолету, требуют защитного лака при наружном применении.
2. Полиэфирные смолы
- Наиболее распространены и дешевле эпоксидных.
- Хорошо подходят для массового производства, быстро отверждаются, устойчивы к коррозии и имеют приемлемую термостойкость.
- Механические свойства хуже, чем у эпоксидных смол.
- Используются в транспортных и строительных профилях, где не требуется высокая прочность.
3. Винилэфирные смолы
- По свойствам занимают промежуточное положение между эпоксидными и полиэфирными.
- Обладают улучшенной ударопрочностью, коррозионной стойкостью и термостойкостью (до 105-121 °С, есть модификации для более высоких температур).
- Хорошо сопротивляются кислотам, щелочам и растворителям.
4. Специализированные смолы
- Фенольные смолы - высокотемпературные, огнестойкие, с хорошей химстойкостью.
- Фурановые смолы - для агрессивных химических сред, выдерживают до 121°С, но требуют аккуратного отверждения.
- Цианат эфирные, полиимидные и бисмалеимидные смолы - для особо высокотемпературных и технически сложных применений.
Вторая часть ответа- завтра.
05.05.202513:52
14.05.202506:03
Ответ на вопрос. Часть 2.
Критерии выбора смолы для углеволоконных композитов
Температура применения
- Для работы при комнатной и умеренных температурах (до 80–120 °C) подходят эпоксидные и полиэфирные смолы.
- Для более высоких температур (до 150–250 °C) рекомендуются модифицированные эпоксидные, винилэфирные, фенольные или специализированные смолы (например, полиимиды, бисмалеимиды).
Нагруженность детали
- При высоких механических нагрузках предпочтительны эпоксидные смолы, обеспечивающие лучшее сцепление с углеволокном и передачу нагрузки.
- Для менее нагруженных конструкций можно использовать полиэфирные смолы, которые дешевле и проще в обработке.
Внешний вид и эстетика
- Эпоксидные смолы дают более гладкую и прозрачную поверхность, хорошо подходят для изделий с высокими требованиями к внешнему виду.
- Полиэфирные смолы могут иметь более матовую поверхность и требуют дополнительной отделки для улучшения внешнего вида.
- Специализированные смолы (например, с добавками для улучшения качества поверхности) используются для изделий с высокими эстетическими требованиями.
Итог
Выбор смолы для работы с углеволокном зависит от конкретных условий эксплуатации и требований к изделию:
- Для высокопрочных, нагруженных и/или высокотемпературных деталей - эпоксидные или специализированные термостойкие смолы.
- Для массового производства и менее нагруженных изделий - полиэфирные или винилэфирные смолы.
- Для изделий с высокими требованиями к внешнему виду - эпоксидные смолы с хорошей прозрачностью и отделкой.
Перед выбором рекомендуется провести испытания выбранной смолы в условиях, максимально приближенных к реальным, чтобы оценить её поведение и свойства в конкретном применении.
Конечно, это не все факторы, которые нужно учитывать при выборе связующего. Чтобы лучше разбираться в вопросе, нужно понимать фундаментальные основы построения композита и алгоритм разработки изделия.
Курс молодого бойца стартует в конце месяца. Рекомендую его изучить и вопросов, что выбрать и как сделать станет меньше.
Критерии выбора смолы для углеволоконных композитов
Температура применения
- Для работы при комнатной и умеренных температурах (до 80–120 °C) подходят эпоксидные и полиэфирные смолы.
- Для более высоких температур (до 150–250 °C) рекомендуются модифицированные эпоксидные, винилэфирные, фенольные или специализированные смолы (например, полиимиды, бисмалеимиды).
Нагруженность детали
- При высоких механических нагрузках предпочтительны эпоксидные смолы, обеспечивающие лучшее сцепление с углеволокном и передачу нагрузки.
- Для менее нагруженных конструкций можно использовать полиэфирные смолы, которые дешевле и проще в обработке.
Внешний вид и эстетика
- Эпоксидные смолы дают более гладкую и прозрачную поверхность, хорошо подходят для изделий с высокими требованиями к внешнему виду.
- Полиэфирные смолы могут иметь более матовую поверхность и требуют дополнительной отделки для улучшения внешнего вида.
- Специализированные смолы (например, с добавками для улучшения качества поверхности) используются для изделий с высокими эстетическими требованиями.
Итог
Выбор смолы для работы с углеволокном зависит от конкретных условий эксплуатации и требований к изделию:
- Для высокопрочных, нагруженных и/или высокотемпературных деталей - эпоксидные или специализированные термостойкие смолы.
- Для массового производства и менее нагруженных изделий - полиэфирные или винилэфирные смолы.
- Для изделий с высокими требованиями к внешнему виду - эпоксидные смолы с хорошей прозрачностью и отделкой.
Перед выбором рекомендуется провести испытания выбранной смолы в условиях, максимально приближенных к реальным, чтобы оценить её поведение и свойства в конкретном применении.
Конечно, это не все факторы, которые нужно учитывать при выборе связующего. Чтобы лучше разбираться в вопросе, нужно понимать фундаментальные основы построения композита и алгоритм разработки изделия.
Курс молодого бойца стартует в конце месяца. Рекомендую его изучить и вопросов, что выбрать и как сделать станет меньше.

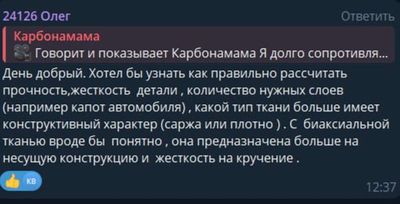
05.05.202513:49
Вопрос №1 от уважаемого карбонария
21.04.202509:03
Встреча с экспертом в закрытом клубе будет в среду, 23 апреля в 18.00 по Москве.
29.04.202509:10
✨ Композитные технологии в сердце Парижа: купола Собора Святой Троицы
На берегу Сены, в 7-м округе Парижа, возвышается Культурно-духовный центр Русской Православной Церкви — с золотыми куполами, которые не просто архитектурное украшение, а технологический вызов.
Что сделали:
Для пяти позолоченных куполов использовали композитные материалы.
Проект реализовали компании Décision SA и Multiplast (в составе Carboman Group).
Поставщик материалов — французская компания Sicomin.
Какие технологии применяли:
Молды для куполов: стеклоткань + бальса, вакуумная инфузия эпоксидной системы Sicomin SR8100/SD7820 с температурой стеклования 120 °C.
Сами купола: вакуумная инфузия эпоксидной смолы Sicomin SR8100/SD4772 с особой стекловолоконной выкладкой.
Использовали тяжёлую квадроксиальную ткань QX1180 + 500 г/м² ткань, чтобы обеспечить идеальное качество поверхности без "эффекта принта".
Почему выбрали композиты:
Лёгкость: значительно снижена нагрузка на здание.
Быстрая установка: купола собирали отдельно, а затем быстро монтировали.
Контроль качества: производство и декорирование в заводских условиях, без влияния погоды.
Оптимизированная термообработка: лабораторные тесты DSC позволили стабилизировать материал перед финальным этапом — нанесением 86 000 листов настоящего золота на поверхность площадью 640 м².
Вывод Карбонамамы:
Когда традиции требуют золота, а технологии — лёгкости и прочности, композиты — это мост между эпохами.
На берегу Сены, в 7-м округе Парижа, возвышается Культурно-духовный центр Русской Православной Церкви — с золотыми куполами, которые не просто архитектурное украшение, а технологический вызов.
Что сделали:
Для пяти позолоченных куполов использовали композитные материалы.
Проект реализовали компании Décision SA и Multiplast (в составе Carboman Group).
Поставщик материалов — французская компания Sicomin.
Какие технологии применяли:
Молды для куполов: стеклоткань + бальса, вакуумная инфузия эпоксидной системы Sicomin SR8100/SD7820 с температурой стеклования 120 °C.
Сами купола: вакуумная инфузия эпоксидной смолы Sicomin SR8100/SD4772 с особой стекловолоконной выкладкой.
Использовали тяжёлую квадроксиальную ткань QX1180 + 500 г/м² ткань, чтобы обеспечить идеальное качество поверхности без "эффекта принта".
Почему выбрали композиты:
Лёгкость: значительно снижена нагрузка на здание.
Быстрая установка: купола собирали отдельно, а затем быстро монтировали.
Контроль качества: производство и декорирование в заводских условиях, без влияния погоды.
Оптимизированная термообработка: лабораторные тесты DSC позволили стабилизировать материал перед финальным этапом — нанесением 86 000 листов настоящего золота на поверхность площадью 640 м².
Вывод Карбонамамы:
Когда традиции требуют золота, а технологии — лёгкости и прочности, композиты — это мост между эпохами.
06.05.202512:12
05.05.202505:00
Проект Carbonhause ( Cube )
Начинаем неделю с обзора применения углеродного волокна в архитектуре:
Местоположение: Дрезден, Германия
Год завершения: 2022
Архитекторы и инженеры: HENN Architekten, Технический университет Дрездена (TU Dresden), Институт прочного строительства под руководством профессора Манфреда Курбаха
Площадь: 220–243 м² (экспериментальное здание, лаборатория и пространство для мероприятий)
Используемые материалы
Углепластик : Армирующая сетка из углеродных волокон, пропитанных термореактивным связующим.
Бетон: Высокопрочный бетон, армированный сеткой из углепластика.
Роль и применение углепластика
Структурное армирование: Вся несущая конструкция здания выполнена с применением сетки из углеродных волокон вместо традиционной стальной арматуры. Это позволило сделать стены и крышу значительно тоньше и легче, чем при использовании стали, сохраняя или превышая прочность.
Органическая форма: Стены плавно переходят в крышу, образуя единую, текучую оболочку - дизайн вдохновлён гибкостью и «текстильной» природой карбоновых волокон. Перегородки и потолок сливаются в органический континуум, а не воспринимаются как отдельные элементы.
Интеграция функций: Благодаря электропроводимости карбона в стены интегрированы нагревательные элементы, сенсорные панели и системы мониторинга состояния конструкции. Это открывает путь к созданию «умных» зданий.
Технологии и методы производства
Префабрикация: Часть здания выполнена из сборных бетонных панелей с интегрированной карбоновой сеткой.
Напыление бетона: Для создания скрученного фасада бетон напылялся на сетку из углеродных волокон, уложенную на фанерную опалубку.
Минимальная толщина: Благодаря отсутствию коррозии у углепластика, защитный слой бетона минимален, что позволяет делать конструкции в 4 раза тоньше и легче традиционных железобетонных аналогов.
Экологичность: Использование армирующей сетки позволяет снизить расход бетона и арматуры примерно на 50%, а выбросы CO₂ - до 50% по сравнению с традиционным строительством.
Инновационные и технические аспекты
Революционная замена стали: Полный отказ от стальной арматуры - впервые в мире для здания такого масштаба.
Долговечность: Ожидаемый срок службы - до 200 лет, благодаря устойчивости к коррозии и высокой прочности.
Формообразование: Свобода в архитектурном выражении - текучие, скрученные формы, невозможные для традиционного бетона.
Потенциал для «умных» зданий: Электропроводимость карбона позволяет интегрировать в стены датчики, системы обогрева и мониторинга.
Вклад в устойчивое строительство: Проект демонстрирует возможности ресурсо- и энергосбережения, а также снижение экологического следа строительной отрасли.
Carbonhaus (Cube) - первое в мире здание, полностью построенное из бетона, армированного углеродным волокном, без использования стали. Это экспериментальное сооружение стало демонстрационным проектом крупнейшей в Германии исследовательской программы C³ – Carbon Concrete Composite, финансируемой государством. Органическая форма здания, где стены и крыша плавно переходят друг в друга, подчёркивает архитектурные возможности нового материала. Проект стал символом технологического прорыва и устойчивого развития в строительстве, открывая путь к более лёгким, долговечным и интеллектуальным зданиям будущего
Начинаем неделю с обзора применения углеродного волокна в архитектуре:
Местоположение: Дрезден, Германия
Год завершения: 2022
Архитекторы и инженеры: HENN Architekten, Технический университет Дрездена (TU Dresden), Институт прочного строительства под руководством профессора Манфреда Курбаха
Площадь: 220–243 м² (экспериментальное здание, лаборатория и пространство для мероприятий)
Используемые материалы
Углепластик : Армирующая сетка из углеродных волокон, пропитанных термореактивным связующим.
Бетон: Высокопрочный бетон, армированный сеткой из углепластика.
Роль и применение углепластика
Структурное армирование: Вся несущая конструкция здания выполнена с применением сетки из углеродных волокон вместо традиционной стальной арматуры. Это позволило сделать стены и крышу значительно тоньше и легче, чем при использовании стали, сохраняя или превышая прочность.
Органическая форма: Стены плавно переходят в крышу, образуя единую, текучую оболочку - дизайн вдохновлён гибкостью и «текстильной» природой карбоновых волокон. Перегородки и потолок сливаются в органический континуум, а не воспринимаются как отдельные элементы.
Интеграция функций: Благодаря электропроводимости карбона в стены интегрированы нагревательные элементы, сенсорные панели и системы мониторинга состояния конструкции. Это открывает путь к созданию «умных» зданий.
Технологии и методы производства
Префабрикация: Часть здания выполнена из сборных бетонных панелей с интегрированной карбоновой сеткой.
Напыление бетона: Для создания скрученного фасада бетон напылялся на сетку из углеродных волокон, уложенную на фанерную опалубку.
Минимальная толщина: Благодаря отсутствию коррозии у углепластика, защитный слой бетона минимален, что позволяет делать конструкции в 4 раза тоньше и легче традиционных железобетонных аналогов.
Экологичность: Использование армирующей сетки позволяет снизить расход бетона и арматуры примерно на 50%, а выбросы CO₂ - до 50% по сравнению с традиционным строительством.
Инновационные и технические аспекты
Революционная замена стали: Полный отказ от стальной арматуры - впервые в мире для здания такого масштаба.
Долговечность: Ожидаемый срок службы - до 200 лет, благодаря устойчивости к коррозии и высокой прочности.
Формообразование: Свобода в архитектурном выражении - текучие, скрученные формы, невозможные для традиционного бетона.
Потенциал для «умных» зданий: Электропроводимость карбона позволяет интегрировать в стены датчики, системы обогрева и мониторинга.
Вклад в устойчивое строительство: Проект демонстрирует возможности ресурсо- и энергосбережения, а также снижение экологического следа строительной отрасли.
Carbonhaus (Cube) - первое в мире здание, полностью построенное из бетона, армированного углеродным волокном, без использования стали. Это экспериментальное сооружение стало демонстрационным проектом крупнейшей в Германии исследовательской программы C³ – Carbon Concrete Composite, финансируемой государством. Органическая форма здания, где стены и крыша плавно переходят друг в друга, подчёркивает архитектурные возможности нового материала. Проект стал символом технологического прорыва и устойчивого развития в строительстве, открывая путь к более лёгким, долговечным и интеллектуальным зданиям будущего
21.04.202505:00
♻️ Пост 1. Рециклинг, но умный
🔥 Новость недели:
Японские учёные предложили малотемпературный способ извлечения углеродных волокон из отходов углепластика.
Секрет — в нагреве до 200 °C в расплаве гидроксида натрия и гидроксида калия (оптимальное соотношение 1:3), что позволяет разрушить термореактивную матрицу без потери прочности волокна.
🧑🔬 Кто сделал:
Takaaki Wajima и Kazuki Yamashita
Кафедра материаловедения, инженерный факультет Университета Тиба (Chiba University), Япония.
Работа опубликована в журнале Scientific Reports.
🧠 Почему это важно:
Проблема переработки углепластика в том, что термореактивная смола не плавится и не даёт “вторую жизнь”.
Этот метод — дешёвый, доступный и щадящий к волокну.
И, в отличие от сжигания или пиролиза, сохраняет прочность волокна, близкую к оригиналу.
📦 Сейчас это:
Лабораторный прототип. Но при масштабировании может кардинально изменить подход к отходам в отрасли.
📍 Где применимо:
Авиастроение, автопром, ветроэнергетика — везде, где углепластик в промышленных масштабах становится мусором.
🌱 Потенциал:
Это шаг к замкнутому циклу карбона.
Меньше отходов. Ниже себестоимость. Больше смысла.
🔥 Новость недели:
Японские учёные предложили малотемпературный способ извлечения углеродных волокон из отходов углепластика.
Секрет — в нагреве до 200 °C в расплаве гидроксида натрия и гидроксида калия (оптимальное соотношение 1:3), что позволяет разрушить термореактивную матрицу без потери прочности волокна.
🧑🔬 Кто сделал:
Takaaki Wajima и Kazuki Yamashita
Кафедра материаловедения, инженерный факультет Университета Тиба (Chiba University), Япония.
Работа опубликована в журнале Scientific Reports.
🧠 Почему это важно:
Проблема переработки углепластика в том, что термореактивная смола не плавится и не даёт “вторую жизнь”.
Этот метод — дешёвый, доступный и щадящий к волокну.
И, в отличие от сжигания или пиролиза, сохраняет прочность волокна, близкую к оригиналу.
📦 Сейчас это:
Лабораторный прототип. Но при масштабировании может кардинально изменить подход к отходам в отрасли.
📍 Где применимо:
Авиастроение, автопром, ветроэнергетика — везде, где углепластик в промышленных масштабах становится мусором.
🌱 Потенциал:
Это шаг к замкнутому циклу карбона.
Меньше отходов. Ниже себестоимость. Больше смысла.
15.05.202508:00
✦ Карбон — это не просто материал. Это отстройка от реальности.
Если ты думаешь, что карбон — просто один из множества материалов, ты занимаешься не своим делом.
Мы слышим это постоянно.
«Ну карбон, углеткань… как стеклоткань, только подороже.»
«Материал как материал, вон у нас и алюминий есть, и титан, и базальт.»
Это говорят те, кто видит в карбоне чёрное волокно — но не видит то, что стоит за ним.
✦ Карбон — это не про материал. Это про прорыв.
Это единственный промышленный материал, который:
летает в космос,
едет в Формуле-1,
ходит в протезах,
и при этом… до сих пор делается руками.
В смысле — вручную. Руки человека выкладывают каждый слой, каждую текстуру, каждый изгиб. Это уже не инженерия. Это ремесло.
Углеродное волокно — это не просто прочность. Это способ сделать невозможное: невесомое — прочным, а жесткое — живым.
✦ Карбон — это улучшение качества жизни, а не просто "прочность на разрыв"
Он позволяет ходить тем, кто потерял ноги.
Делает рамы велосипедов легче, чем мечты подростка.
Даёт структуру спутникам, которые уходят за пределы Солнечной системы.
Помогает строить город внутри дрона, реактора, капсулы.
Покажите мне другой материал, который делает и искусство, и имплант, и крыло, и скелет экзокостюма.
Карбон не решает одну задачу — он меняет само поле игры.
✦ Другие материалы строят.
Карбон — двигает.
Он не поддаётся стандартизации. Не прощает ошибок. Требует головы и рук.
Именно поэтому он разделяет мир на тех, кто умеет — и тех, кто просто называет себя производителем.
Если ты смотришь на карбон и видишь просто один из материалов — ты не понял, что у тебя в руках.
Карбон — это не про "чем заменить". Это про "зачем вообще менять?"
И последнее.
Если ты действительно думаешь, что карбон — просто материал, один из многих,
ты занимаешься не своим делом.
Потому что в этом деле — только одержимые.
Если ты думаешь, что карбон — просто один из множества материалов, ты занимаешься не своим делом.
Мы слышим это постоянно.
«Ну карбон, углеткань… как стеклоткань, только подороже.»
«Материал как материал, вон у нас и алюминий есть, и титан, и базальт.»
Это говорят те, кто видит в карбоне чёрное волокно — но не видит то, что стоит за ним.
✦ Карбон — это не про материал. Это про прорыв.
Это единственный промышленный материал, который:
летает в космос,
едет в Формуле-1,
ходит в протезах,
и при этом… до сих пор делается руками.
В смысле — вручную. Руки человека выкладывают каждый слой, каждую текстуру, каждый изгиб. Это уже не инженерия. Это ремесло.
Углеродное волокно — это не просто прочность. Это способ сделать невозможное: невесомое — прочным, а жесткое — живым.
✦ Карбон — это улучшение качества жизни, а не просто "прочность на разрыв"
Он позволяет ходить тем, кто потерял ноги.
Делает рамы велосипедов легче, чем мечты подростка.
Даёт структуру спутникам, которые уходят за пределы Солнечной системы.
Помогает строить город внутри дрона, реактора, капсулы.
Покажите мне другой материал, который делает и искусство, и имплант, и крыло, и скелет экзокостюма.
Карбон не решает одну задачу — он меняет само поле игры.
✦ Другие материалы строят.
Карбон — двигает.
Он не поддаётся стандартизации. Не прощает ошибок. Требует головы и рук.
Именно поэтому он разделяет мир на тех, кто умеет — и тех, кто просто называет себя производителем.
Если ты смотришь на карбон и видишь просто один из материалов — ты не понял, что у тебя в руках.
Карбон — это не про "чем заменить". Это про "зачем вообще менять?"
И последнее.
Если ты действительно думаешь, что карбон — просто материал, один из многих,
ты занимаешься не своим делом.
Потому что в этом деле — только одержимые.
07.05.202505:00
🔬 Переработка углепластика: Fraunhofer и российский контекст
1. Германия: Fraunhofer EMI
Институт Fraunhofer EMI разработал лазерную технологию локального пиролиза для извлечения непрерывных углеродных волокон из термореактивных композитов без потери механических свойств.
Метод особенно эффективен для переработки намотанных конструкций (например, водородных баллонов).
Ключевые особенности:
локальное нагревание до 300–600 °C без разрушения волокна;
одновременное разложение смолы и размотка волокна;
энергозатраты в 5 раз ниже по сравнению с производством нового волокна.
Проект реализуется в рамках DigiTain до конца 2025 года при поддержке Министерства экономики и защиты климата Германии.
🇷🇺 2. Россия: что происходит у нас
В России формируется собственная экосистема для устойчивой переработки углепластиков, включая разработки научных институтов, промышленные проекты и национальные программы.
🔬 Исследования и технологии
ВИАМ изучает технологии пиролиза и совмещения переработки с цементными печами. Анализируются и международные практики.
РНФ поддерживает проекты по созданию сорбентов из углеродосодержащих отходов, что может быть применено в рециклинге композитов.
Балтийский федеральный университет разрабатывает сольволиз для удаления смол (до 98%) и сохранения углеродных волокон.
МГТУ им. Баумана занимается самовосстанавливающимися и перерабатываемыми композитами.
🏭 Промышленность
UMATEX (Росатом): проект по рециклингу композитов в нетканые материалы, мощность — 150 тонн в год (завод ЗУКМ).
ВУХИН: технология переработки углепластиков в среде кокса — термическая утилизация с сохранением структуры волокна.
ЭкоЛайн: развивает инфраструктуру сортировки отходов в рамках циркулярной экономики, потенциально поддерживая композитную переработку.
📑 Государственные программы
Нацпроект «Экология» предполагает 100% сортировку ТКО к 2030 году и создание заводов по извлечению ценных компонентов из отходов.
Повестка до 2025 года делает акцент на замкнутом цикле и повторном использовании сложных материалов в высокотехнологичных отраслях, включая авиастроение.
🧩 Вывод:
Переработка углепластика становится стратегическим направлением и в Европе, и в России.
Если Fraunhofer даёт технологический прорыв в пиролизе, то в России параллельно развиваются инженерные, химические и промышленные решения — от сольволиза до нетканых материалов. Всё это — шаг к устойчивой и экономически эффективной переработке сложных композитов в реальном производстве.
1. Германия: Fraunhofer EMI
Институт Fraunhofer EMI разработал лазерную технологию локального пиролиза для извлечения непрерывных углеродных волокон из термореактивных композитов без потери механических свойств.
Метод особенно эффективен для переработки намотанных конструкций (например, водородных баллонов).
Ключевые особенности:
локальное нагревание до 300–600 °C без разрушения волокна;
одновременное разложение смолы и размотка волокна;
энергозатраты в 5 раз ниже по сравнению с производством нового волокна.
Проект реализуется в рамках DigiTain до конца 2025 года при поддержке Министерства экономики и защиты климата Германии.
🇷🇺 2. Россия: что происходит у нас
В России формируется собственная экосистема для устойчивой переработки углепластиков, включая разработки научных институтов, промышленные проекты и национальные программы.
🔬 Исследования и технологии
ВИАМ изучает технологии пиролиза и совмещения переработки с цементными печами. Анализируются и международные практики.
РНФ поддерживает проекты по созданию сорбентов из углеродосодержащих отходов, что может быть применено в рециклинге композитов.
Балтийский федеральный университет разрабатывает сольволиз для удаления смол (до 98%) и сохранения углеродных волокон.
МГТУ им. Баумана занимается самовосстанавливающимися и перерабатываемыми композитами.
🏭 Промышленность
UMATEX (Росатом): проект по рециклингу композитов в нетканые материалы, мощность — 150 тонн в год (завод ЗУКМ).
ВУХИН: технология переработки углепластиков в среде кокса — термическая утилизация с сохранением структуры волокна.
ЭкоЛайн: развивает инфраструктуру сортировки отходов в рамках циркулярной экономики, потенциально поддерживая композитную переработку.
📑 Государственные программы
Нацпроект «Экология» предполагает 100% сортировку ТКО к 2030 году и создание заводов по извлечению ценных компонентов из отходов.
Повестка до 2025 года делает акцент на замкнутом цикле и повторном использовании сложных материалов в высокотехнологичных отраслях, включая авиастроение.
🧩 Вывод:
Переработка углепластика становится стратегическим направлением и в Европе, и в России.
Если Fraunhofer даёт технологический прорыв в пиролизе, то в России параллельно развиваются инженерные, химические и промышленные решения — от сольволиза до нетканых материалов. Всё это — шаг к устойчивой и экономически эффективной переработке сложных композитов в реальном производстве.
01.05.202505:00
🚀 Foilone PEGASUS: когда углепластик летает над водой
Foilone PEGASUS — это не просто лодка. Это персональный гидрофойл-аппарат нового поколения. И, конечно, на 100% из углеродного волокна. 🖤
📍 Кто разработал:
Компания Foilone (Финляндия)
Инженерия и дизайн вдохновлены авиацией и болидами Формулы-1
🌊 Где применяется:
Спорт и активный отдых
Персональный транспорт на воде
Для тех, кто хочет "летать" над водой без лишнего шума и следов 🌬
🛠 Из чего сделан PEGASUS:
Корпус, гидрофойлы, мачта, все несущие элементы — углеродное волокно
Используются высокоточные технологии композитного производства: вероятно, препреги, автоклав или вакуумная инфузия
🎯 Результат: ультра-лёгкий, жёсткий и выносливый корпус.
⚙️ Технические характеристики:
Электродвигатель: 18,8 кВт (~25 л.с.) ⚡️
Два аккумулятора Torqeedo по 5 кВт·ч
Полная зарядка: менее 2 часов
Крейсерская скорость: 33–41 км/ч
Максимальная скорость: 55 км/ч 🚀
Запас хода: более 2 часов
Масса: 200 кг (с батареями), 128 кг (без батарей)
Длина: 4,88 м | Ширина: 0,95 м | Осадка: 1 м (с фойлами)
✨ Особенности конструкции:
Гидрофойлы поднимают лодку над водой — меньше сопротивления, выше скорость, больше кайфа.
Минималистичный дизайн + премиальная отделка
Интуитивное управление: подходит и новичкам, и профи
Почти бесшумная работа двигателя
Безопасность: автоторможение, осушитель, аварийное весло
🖤 Преимущества углепластика:
Лёгкость для транспортировки и быстрого старта
Жёсткость и прочность для контроля на высоких скоростях
Устойчивость к усталости и коррозии — подходит даже для солёной воды
Энергоэффективность: больше скорости, меньше расхода ⚡️
🌍 Экологичность:
Полностью электрическая силовая установка
Нулевые выбросы
Минимальный след на воде
🎯 Вывод Карбонамамы:
Foilone PEGASUS — это не просто лодка.
Это ощущение полёта над водой, умноженное на технологии углеродного века.
Красиво. Быстро. Чисто.
Foilone PEGASUS — это не просто лодка. Это персональный гидрофойл-аппарат нового поколения. И, конечно, на 100% из углеродного волокна. 🖤
📍 Кто разработал:
Компания Foilone (Финляндия)
Инженерия и дизайн вдохновлены авиацией и болидами Формулы-1
🌊 Где применяется:
Спорт и активный отдых
Персональный транспорт на воде
Для тех, кто хочет "летать" над водой без лишнего шума и следов 🌬
🛠 Из чего сделан PEGASUS:
Корпус, гидрофойлы, мачта, все несущие элементы — углеродное волокно
Используются высокоточные технологии композитного производства: вероятно, препреги, автоклав или вакуумная инфузия
🎯 Результат: ультра-лёгкий, жёсткий и выносливый корпус.
⚙️ Технические характеристики:
Электродвигатель: 18,8 кВт (~25 л.с.) ⚡️
Два аккумулятора Torqeedo по 5 кВт·ч
Полная зарядка: менее 2 часов
Крейсерская скорость: 33–41 км/ч
Максимальная скорость: 55 км/ч 🚀
Запас хода: более 2 часов
Масса: 200 кг (с батареями), 128 кг (без батарей)
Длина: 4,88 м | Ширина: 0,95 м | Осадка: 1 м (с фойлами)
✨ Особенности конструкции:
Гидрофойлы поднимают лодку над водой — меньше сопротивления, выше скорость, больше кайфа.
Минималистичный дизайн + премиальная отделка
Интуитивное управление: подходит и новичкам, и профи
Почти бесшумная работа двигателя
Безопасность: автоторможение, осушитель, аварийное весло
🖤 Преимущества углепластика:
Лёгкость для транспортировки и быстрого старта
Жёсткость и прочность для контроля на высоких скоростях
Устойчивость к усталости и коррозии — подходит даже для солёной воды
Энергоэффективность: больше скорости, меньше расхода ⚡️
🌍 Экологичность:
Полностью электрическая силовая установка
Нулевые выбросы
Минимальный след на воде
🎯 Вывод Карбонамамы:
Foilone PEGASUS — это не просто лодка.
Это ощущение полёта над водой, умноженное на технологии углеродного века.
Красиво. Быстро. Чисто.

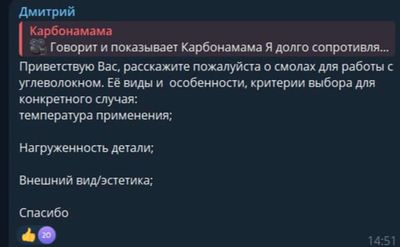
13.05.202513:04
Вопрос от подписчика, ответ на который я задолжала.
Log in to unlock more functionality.